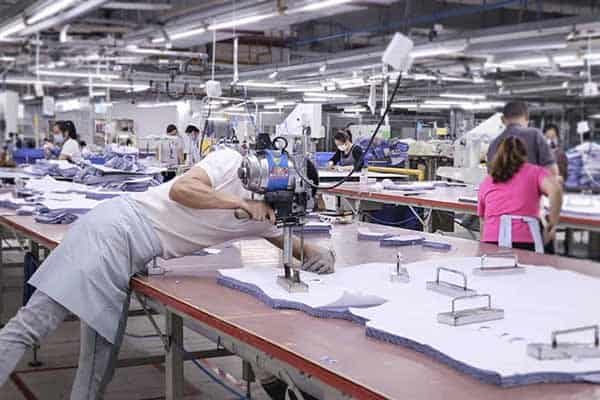
Creating a high-quality golf polo shirt requires meticulous attention to detail at every stage of production. From selecting the right materials to final packaging, every step influences the shirt's performance, durability, and overall aesthetic appeal.
Golf polo shirts are manufactured through a multi-step process that ensures durability, breathability, and comfort. Key stages include material selection, fabric treatment, pattern making, sewing, logo application, quality control, and packaging. Each phase is essential for producing high-performance golf apparel.
Understanding these steps can help buyers and brands make informed decisions when sourcing golf apparel.
Material Selection
The first and most crucial step in manufacturing golf polo shirts is selecting the right fabric. Given that golf is played in various weather conditions, the fabric must be breathable, moisture-wicking, and durable. The most commonly used materials include:
- Polyester blends – Known for their moisture-wicking properties and durability.
- Cotton blends – Offer comfort and breathability but may lack moisture control.
- Spandex-infused fabrics – Provide stretchability for enhanced mobility.
Fabric Treatment and Preparation
Before cutting, the selected fabric undergoes several treatments to enhance performance:
- Moisture-wicking treatment – Improves sweat absorption and quick drying.
- UV protection coating – Shields golfers from harmful sun exposure.
- Antimicrobial treatment – Prevents odor buildup from sweat.
- Pre-shrinking – Ensures minimal fabric shrinkage after washing.
Pattern Making and Cutting
Precision in pattern making is vital to achieving a perfect fit. The process involves:
- Creating a template based on standard or custom sizing.
- Using computer-aided design (CAD) software for accuracy and efficiency.
- Cutting the fabric with laser or blade cutting machines to maintain consistency and reduce waste.
Sewing and Assembly
After cutting, the panels are stitched together following a systematic process:
- Shoulder seams are sewn first to ensure structural integrity.
- Collar and placket attachment using reinforced stitching for durability.
- Sleeve attachment and side seam stitching to complete the basic structure.
- Hem finishing with double-stitched seams to prevent fraying.
Logo Embroidery and Printing
Branding is essential in golf apparel, and logos are added using:
- Embroidery – Preferred for a premium look and durability.
- Heat transfer printing – Suitable for detailed and colorful logos.
- Screen printing – Cost-effective for bulk production.
Quality Control and Inspection
Each golf polo shirt undergoes stringent quality checks, including:
- Fabric inspection – Ensures no defects like holes or stains.
- Stitching inspection – Checks for loose threads and even seams.
- Fitting and measurement validation – Confirms adherence to size charts.
- Color fastness test – Ensures that dyes do not bleed or fade over time.
Packaging and Distribution
Once approved, the shirts are folded, packed, and distributed. Packaging considerations include:
- Eco-friendly packaging – To align with sustainable practices.
- Customized packaging – Enhances brand appeal and customer experience.
- Bulk vs. individual packaging – Depending on the retailer or distributor's requirements.
Industry Insights and Trends
- Sustainability: More brands are shifting towards recycled polyester and biodegradable packaging.
- Smart textiles: Innovations include UV-reactive materials and temperature-regulating fabrics.
- Customization: Demand for personalized golf apparel is rising, with brands offering tailored fits and design options.
By refining each stage of the manufacturing process, brands can produce high-quality golf polo shirts that meet both functional and aesthetic demands, ultimately enhancing golfers’ performance and comfort on the course.parel that stands out in the market.