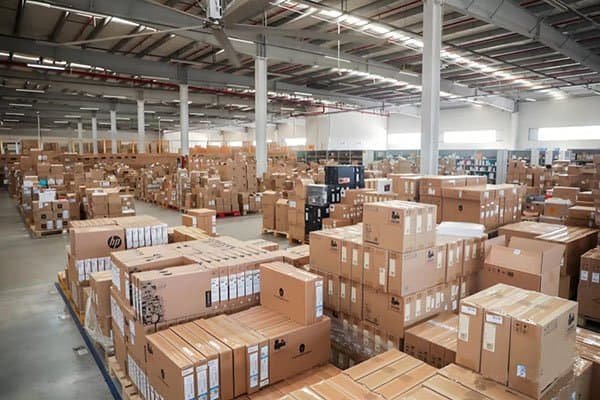
Golf apparel production lead time can make or break your brand’s ability to meet demand. If your delivery time is too long, customers may lose interest or turn to competitors. So, how can you speed things up without sacrificing quality?
Shortening golf apparel production lead time involves optimizing fabric sourcing, pre-approving designs, streamlining manufacturing, reducing quality control delays, and improving logistics. Brands can work closely with suppliers, standardize processes, and leverage faster shipping options to cut weeks off their production cycle, ensuring quicker market delivery.
Let’s break it down step by step.
Optimize Fabric Sourcing & Inventory
Fabric delays are one of the biggest reasons for long lead times. Without proper planning, you could be stuck waiting weeks for materials.
Establish strong relationships with reliable fabric suppliers, pre-order high-demand fabrics, and maintain a buffer stock. Consider working with mills that offer just-in-time production or stock service programs. By securing fabric in advance, you can eliminate major sourcing delays.
(1)Work with Reliable Suppliers
Finding trusted suppliers with a fast turnaround is crucial. Look for mills that have:
- Stock service programs – Ready-to-ship fabrics that reduce waiting time.
- Just-in-time production – Quick production cycles to meet demand.
- Good communication – A supplier that responds quickly can save you days or even weeks.
(2)Keep a Fabric Buffer Stock
If you produce the same or similar designs regularly, keeping extra fabric on hand can prevent delays. Work with your supplier to store frequently used materials for immediate availability.
(3)Pre-Approve Fabrics & Trims
Pre-selecting and approving fabrics ahead of time prevents back-and-forth approval delays. Have a set of go-to materials that your brand consistently uses, so you don’t have to start from scratch each time.
Pre-Approve Designs & Patterns
Waiting for design approvals can create significant bottlenecks. The more revisions and back-and-forth you have, the longer the production cycle.
(1)How to speed up design approvals?
Lock in final designs before production starts. Work with your manufacturer to create pre-approved patterns, colors, and embroidery designs to minimize last-minute changes. Using digital 3D samples can also reduce the need for physical prototypes, cutting down waiting time.
(2)Set Up a Standardized Approval Process
- Approve colors, trims, and prints in bulk before placing orders.
- Use 3D rendering software for virtual samples.
- Keep a master list of pre-approved designs and materials.
Streamline Manufacturing Processes
Once production begins, any inefficiencies in the manufacturing process will slow things down. Lean production strategies can help.
(1)How to streamline the manufacturing process?
Implement lean manufacturing techniques, reduce unnecessary steps, and invest in modern machinery. Ensure that your factory follows a well-organized workflow and uses efficient sewing and cutting methods to speed up production without compromising quality.
(2)Lean Manufacturing Strategies
Strategy | Benefit |
---|---|
Modular production lines | Speeds up assembly and reduces errors |
Automation & AI tools | Cuts down manual work and increases precision |
Batch production | Reduces setup time and material wastage |
Reduce Quality Inspection Bottlenecks
Quality control is necessary, but it shouldn’t slow down your entire process. Poor planning or slow inspection methods can add days to your timeline.
How to speed up quality inspections?
Adopt real-time quality monitoring, conduct in-line inspections instead of waiting until the end, and use automated quality control systems to detect defects faster.
Proactive Quality Control Measures
- In-line inspections – Catch defects early instead of waiting until the end.
- Third-party QC teams – Having external experts ready can speed up approval times.
- AI-powered defect detection – Some manufacturers use AI to scan for defects in real time.
Optimize Logistics & Shipping
Even after production is done, poor logistics planning can cause unexpected delays.
How to optimize logistics and shipping?
Work with multiple freight partners, plan shipments in advance, and use express services when needed. Choose shipping routes that minimize delays, and consider air freight for urgent orders.
Faster Shipping Strategies
- Use multiple freight options – Have backups in case of shipping issues.
- Work with logistics partners offering priority services – This can cut delivery time significantly.
- Plan shipments in batches – Consolidate shipments to save on costs and reduce transit times.
Conclusion
Speeding up golf apparel production requires careful planning, reliable suppliers, efficient manufacturing, and optimized logistics. By addressing these key areas, you can reduce lead times and ensure your products hit the market faster without sacrificing quality.